Use of AI in Manufacturing Industry
With continuous advancements in Artificial Intelligence (AI), the manufacturers are spearheading to apply it in their manufacturing processes to boost product quality, operational efficiency, workforce safety, and many more.
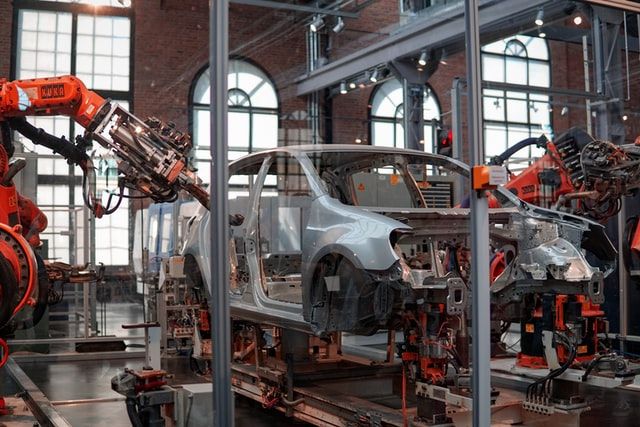
AI being a revolutionary technology for virtually every industry worldwide has been a buzzword for the last few years. With time it is becoming easily accessible for all industries. At present, it is hard-pressed to name any industry that is not enjoying the paybacks from AI in terms of increased value and revenues. One such industry where AI is heavily used is the manufacturing sector. It has been estimated that the worldwide AI in the manufacturing market size will hit $USD 4,798 million by 2026 that was just 840 million in 2019, while CAGR will reach at 28.1% during 2021-2026.
The manufacturing industry is always enthusiastic to embrace advanced technologies. Since the invention of steam-powered machines, the main emphasis of any manufacturing industry is on offering improved products by automating processes. With continuous advancements in AI, the manufacturers are spearheading to apply it in their manufacturing processes to boost product quality, operational efficiency, workforce safety, and many more. As per the Annual Manufacturing Report published in 2018, 92% of manufacturing executives claim that AI has the potential to boost their productivity and authorize the workforce for smart work. At present, the search for “AI in manufacturing” is among the top Google trends. A survey conducted by Deloitte revealed that 93% of manufacturing companies consider AI a decisive technology to achieve substantial growth and innovation, hence AI is being used to transform conventional manufacturing processes to get incremental business outcomes.
The manufacturers having vision and technology like AI that is responsive enough to get the most out of incipient opportunities have a competitive edge and are positioned as leaders. In this article, we will discuss how the use of AI in modern manufacturing, can revolutionize the industry.
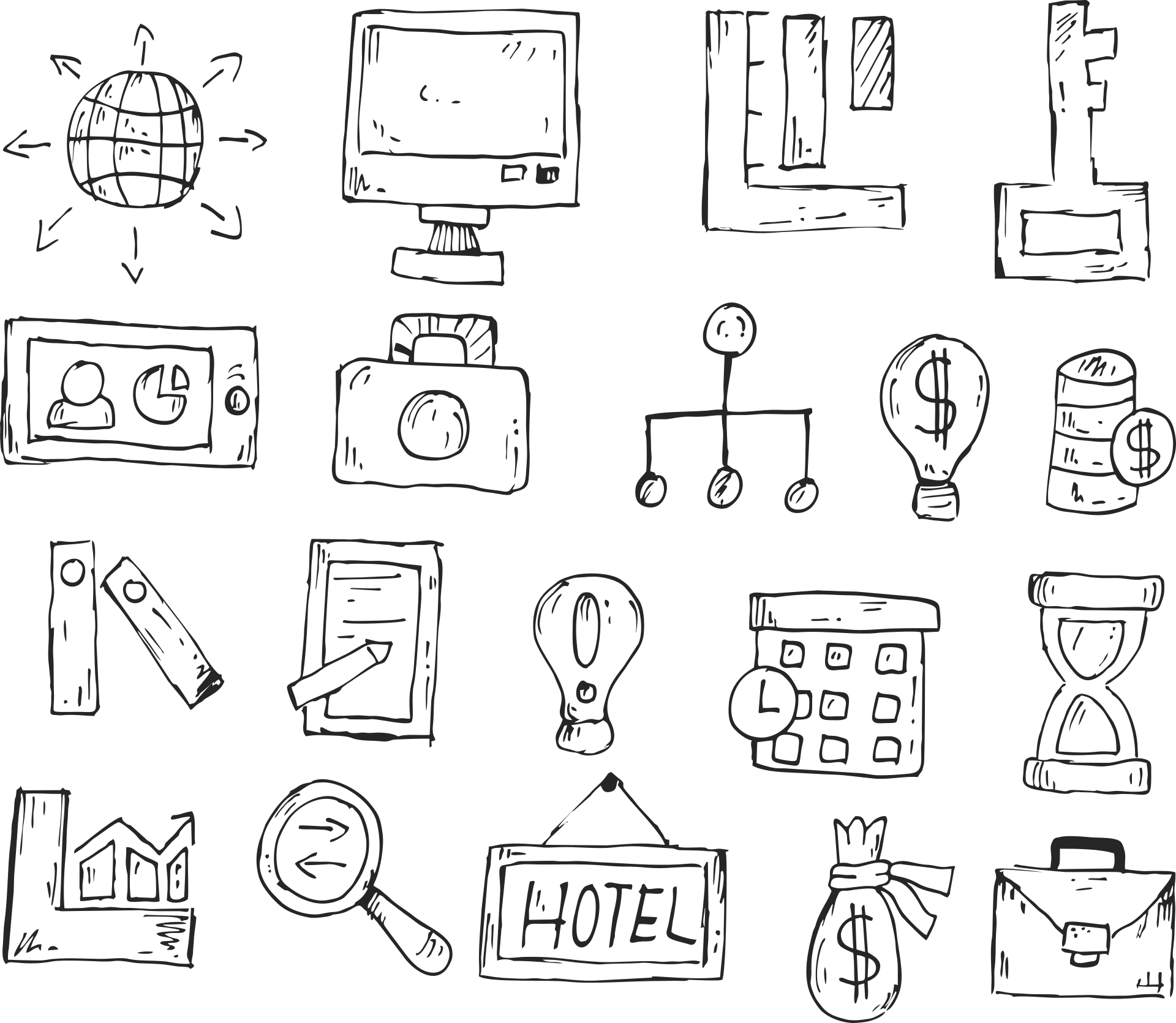
What is stimulating manufacturers to adopt AI?
A manufacturing industry produces data more than any other industry. At present, terabytes of data flow are providing extensive information from virtually every tool on the production floor. Unfortunately, most of the manufacturing industries don't know what to do with this information as they don't have enough resources to decode this extensive information. Ultimately, most of the data is lost. This is the context, where AI raises a hand to offer the solution. AI, having the potential to deal with the full value of gigantic data, helps the manufacturers in decision making, resulting in increased productivity by increasing efficiency and decreasing overall cost. Hence, AI offers an all-in-one solution to the manufacturers to manage enterprise data and processes as well. Simply put, on account of its complex algorithms, improved processing, and capability to hold gigantic data, AI has the potential to revolutionize the manufacturing sector.
Keeping this fact in mind, the worldwide implementation of AI in manufacturing industries is prevailing with time. According to Capgemini, European manufacturers are spearheading the use of AI with 51%, followed by Japan where 30% of manufacturers are employing AI, and the US where this ratio is 28%.
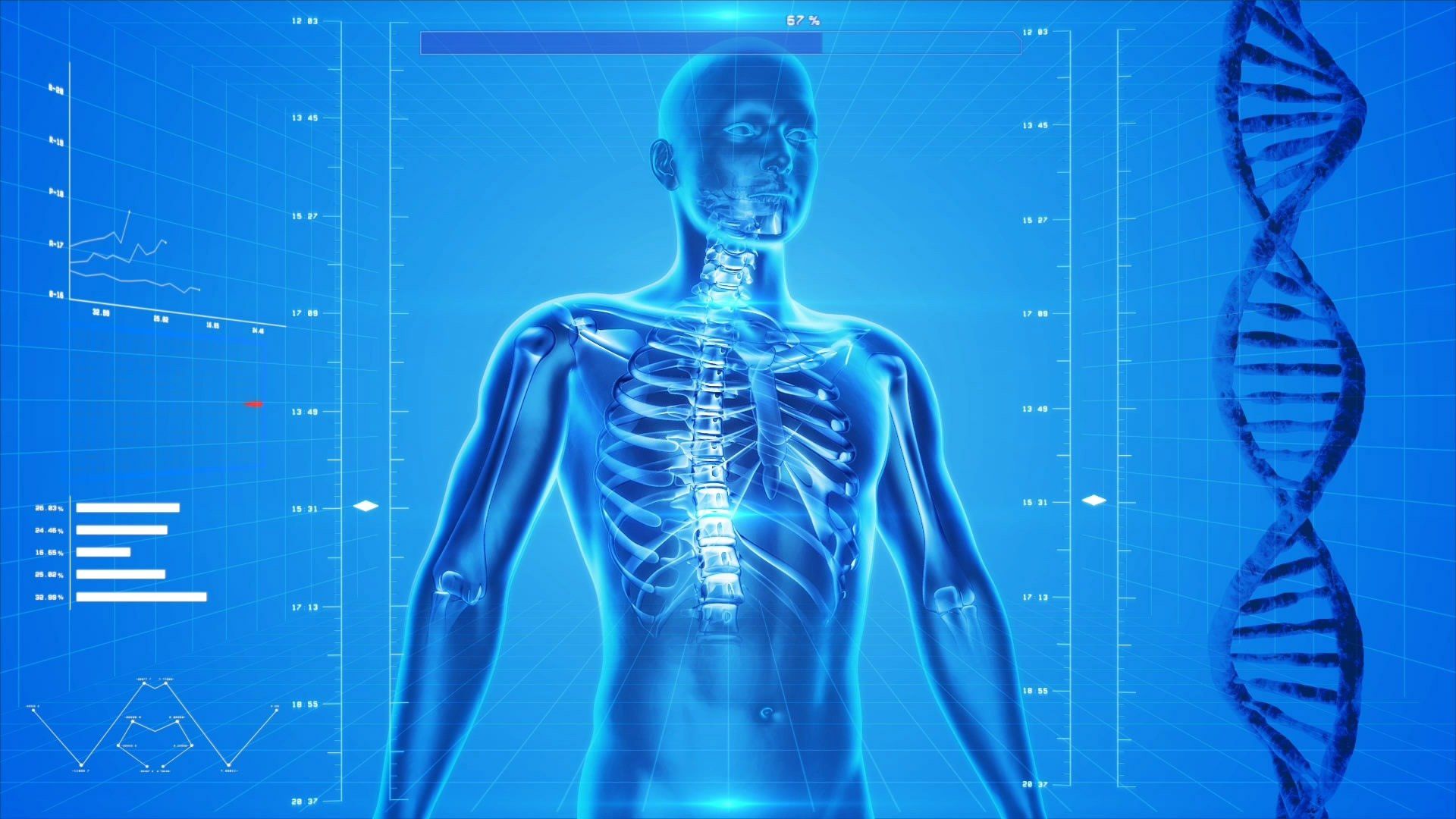
Challenges faced by Manufacturing Industries
The manufacturing industry is habitually facing a wide range of challenges. However, the most significant challenges are:
- Unpredicted machinery failure
- Substandard/Malfunctioned Product delivery
Companies are now employing a wide range of ML and AI solutions to encounter these manufacturing challenges.
AI Solutions to Manufacturing Industries
Today, most of the equipment used in the manufacturing industry sends gigantic data to the cloud. If a manufacturing industry lacks AI implementation, most of this information is not interpreted accurately and remains siloed. However, by Smart Manufacturing i.e., integrating AI with IoT, this data can be easily pulled and interpreted ensuring a clearer view of the operation. Moreover, by integrating AI into the IoT ecosystem, the manufacturers can generate numerous automation. For instance, it sends an automatic notification to the supervisors if any machinery operator is feeling fatigued or exhausted. Similarly, in case of breakage of any machinery part, the system automatically generates an emergency plan to avoid and optimize any haphazard activity. Hence, Smart Manufacturing is proving itself very helpful through automation. According to TrendForce, Smart Manufacturing will grow enormously within the next five years.
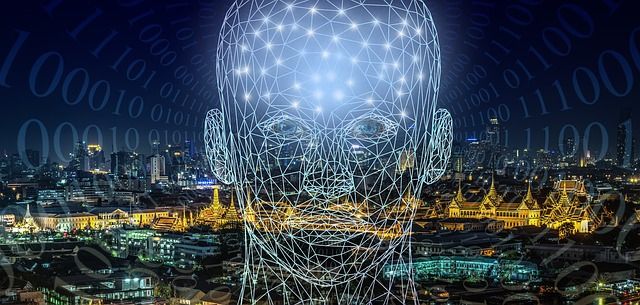
In a manufacturing industry, the product, equipment/asset, and supply chain management are the most crucial factors having a far-reaching impact on the success of a business. According to a study conducted by Capgemini, by employing AI solutions, 29% improvement in equipment maintenance and 27% in product quality are observed. To have a positive impact, the foremost AI transformation objectives are to bring improvement in product quality, maintenance of the machinery, and supply chain management. Let's have a detailed view of how AI is augmenting manufacturing by upgrading these factors:
Product Quality Assurance through Image Recognition Software
Customer satisfaction is a key to success for any manufacturing company. When it's about pleasing customers, the most significant thing is to offer the highest standard product by ensuring its quality at each step of manufacturing. AI helps the manufacturing industry to ensure a high-quality product by using image-recognition software in the following ways:
Real-time In-line Inspection of the Product
Identifying the defects in the production line is very crucial for any manufacturing company. AI helps the manufacturers in real-time analysis of images in quality inspection of the products. With the improvement in AI-driven software of image recognition, high-resolution cameras are getting available at a cheap price. Machines equipped with highly sensitive cameras can easily find out the product flaws in an ongoing process. Contrary, the manufacturers, who lack autonomous defect detection and have on-site employees to check the products manually, are mostly unsuccessful to satisfy the customers as most of these defects are too small to be observed with the naked eye. Based on these factors, real-time inline inspection is becoming very common in manufacturing industries. Audi is spearheading to adopt the technologies with DL-based image recognition system installed at Ingolstadt press shop.
Real-time Inspection of Employees
AI algorithm of machine vision for image processing employs high-quality cameras installed at main locations along the factory floor to detect any abnormal behavior of the employees.
Equipment’s Smart Maintenance through Predictive Analytics
Equipment is the most significant part of an asset-based production operation and its maintenance requires big-budget in a manufacturing industry. A survey by ServiceMax revealed that the cost of unplanned machinery downtime for factories is roughly $50 billion of which 42% is due to asset failure. Manufacturers endeavor to ensure that their facility and machinery remain operational. In this context, AI-based predictive maintenance is the most promising solution that is cost-effective as well. That is why the manufacturing companies are now shifting from responsive maintenance to predictive maintenance with the help of AI and ML. AI algorithms like ML and Neural Networks provide trustworthy status predictions of machines and assets. The maintenance managers integrate data from sensors and machines and can predict the possible time for eminent failure of machinery. Hence, With AI, the RUL (Remaining Useful Life) of equipment is getting longer as it enables the technicians to beforehand identification of repair or replacement need of the equipment and also proposes the solution and ideal time to fix the issue.
As per McKinsey & Company, the use of predictive maintenance technologies has resulted in a 20% decline in the maintenance cost, and a 50% reduced unexpected outages. It also extends the lifespan of machines by years. A large number of manufacturing companies, including Siemens and LG are using predictive maintenance. Ronald Busch, from Siemens, states:
"By analyzing the data, our AI systems can conclude a machine's condition and detect irregularities to make predictive maintenance possible.”
In the manufacturing industry, 29% of implementations of AI are to maintain machinery and production resources. According to Capgemini, the most significant use cases of AI to improve manufacturing are anticipating the time of machinery failure and recommending the ideal maintenance time. Predictive maintenance helps in reducing operational cost; let’s have a look at how it works:
Reduced Operational Cost
AI believes in predictive maintenance that in turn reduces the operational cost by reducing the machine downtime. In this digital era, the demand for more personalized and customized products is increasing. ML and AI-based Generative Design help in meeting these needs of the customers more cost-effectively. By using both of these AI applications, the systems are first designed and checked in a virtual model. If they work efficiently, then their actual production starts. Let’s have a look at how both of these AI applications work to reduce the overall operational cost:
Generative Design is AI-driven software using neural networks to produce multiple outputs to meet required standards. In the generative design algorithm of AI, an engineer or designer feeds the design goals. This algorithm, after looking for all the probable transformations, generates an alternative design. The proposed solutions are then put in ML algorithm for additional insight on the best workable design. This process is repeated several times to get an optimal design solution ultimately. All of this process helps to reduce the trial-and-error cost of machine testing which in turn reduces the operational cost of the manufacturing industry.
For engineers, generative design is an excellent way to design a great number of possibilities. Hence AI comes up with quick and efficient ideas to meet the customer needs while reducing the operational cost.
Supply Chain Management
One of the essential components for a manufacturing industry is Supply Chain Management. Luckily, the use of AI is not restricted to the production floor for product quality assurance and predictive maintenance of equipment, but it also helps in supply chain management through anticipating market changes. Sourcing raw materials and efficient logistics handling are very crucial for a manufacturing company. There are multiple materials, purchases, and orders in a supply chain to manage on a routine basis. Manual handling of the supply chain is hectic and time-taking. With the use of AI applications like ML and NLP, manufacturers are now having smarter systems for the supply chain management. We have explained below how AI helps manufacturers in improving the supply chain:
Improved Supply Planning and Demand Forecast
ML is very helpful in forecasting supply planning while demand forecasting tools of AI are extremely beneficial to offer more accurate results as compared to conventional methods. AI algorithms project market demands by analyzing consumer behavior and hence improve the accuracy of demand forecasts. For instance, predictive analytics algorithms used to analyze buying patterns of the consumers can stimulate manufacturers to upgrade or lower the production of an individual product and accordingly plan for its supply in the market.
The manufacturers of Consumer Packaged Goods are spearheading in employing AI for this purpose and are getting solid results. A French-based manufacturer of food products named “Danone Group,” is deploying an ML system to enhance planning coordination across different departments including sales and marketing, finance, and supply chain, and hence upgrading the accuracy of demand forecast. By adopting this AI system, the company's forecast error and product obsolescence have reduced to 20% and 30% respectively. This system has also led to the reduction of 30% in lost sales and 50% in the workload of demand planners.
Inventory Management
Based on demand forecast, the manufacturers manage beforehand inventory of the product that could be high in demand in the future. Hence AI provides manufacturing companies with the best tools to optimize inventory levels more exceptionally.
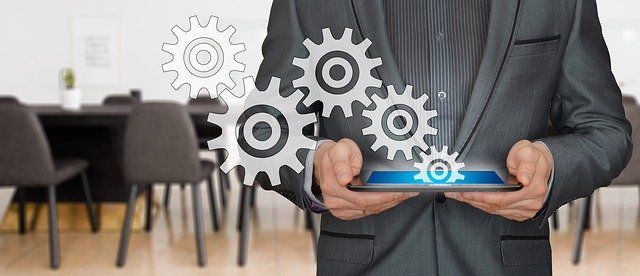
Additional benefits of employing AI in Manufacturing Company
AI, besides real-time monitoring of product, equipment, and supply chain, also benefits a manufacturing company in the following ways:
Improved Decision making through Digital Twinning – AI helps a manufacturer in prompt and improved decision making through Digital Twins. It refers to the virtual demonstration of a factory or product that counterpart the physical aspects of its real-world by using cameras, sensors, and other data collection procedures. Bernard Marr states:
“The pairing of the virtual and physical worlds allows analysis of data and monitoring systems to head off problems before they even occur, prevent downtime, develop new opportunities and even plan for the future by using simulations.”
Digital Twins is used by a manufacturing company to make decisions that are model-driven. According to a Gartner survey conducted in 2019, 13% of organizations were using digital twins, while 62% were ambitious to use them within a year.
Reduced Environmental Impact
Several manufacturing companies like Electronics continue to adversely affect the environment. For lithium-ion batteries, several minerals like cobalt, nickel, and graphite are extracted. This extraction enhances the production of plastic and e-waste along with extensive energy consumption. According to Jahda Swansborough, AI is very helpful to reduce or even reverse the environmental impact, revolutionizing the manufacturing industry. Moreover, AI is also helpful in creating eco-friendly materials and boosting energy efficiency.
AI-driven Robots to improve overall productivity
Cobots –collaborative robots are becoming very popular in manufacturing industries. These Cobots work in close collaboration with humans, following their instructions to enhance the productivity of the system. In certain areas, robots are more efficient than humans like in assembly lines, picking, and packaging. Humans get tired of the monotonous tasks and need rest and frequent maintenance in the form of food and sleep. Contrary, AI-driven robots are never tired or hungry and can work 24/7 on the production line, hence increase the production capabilities of the industry to meet the growing need of customers across the globe.
Moreover, humans are prone to mistakes whereas robots are not. In the manufacturing industry, AI enables remote access control; hence reduce human resources particularly in hazardous tasks when superhuman efforts are required. Not just the hazardous tasks, but the regular tasks are also improved due to reduced occurrence of incidents.
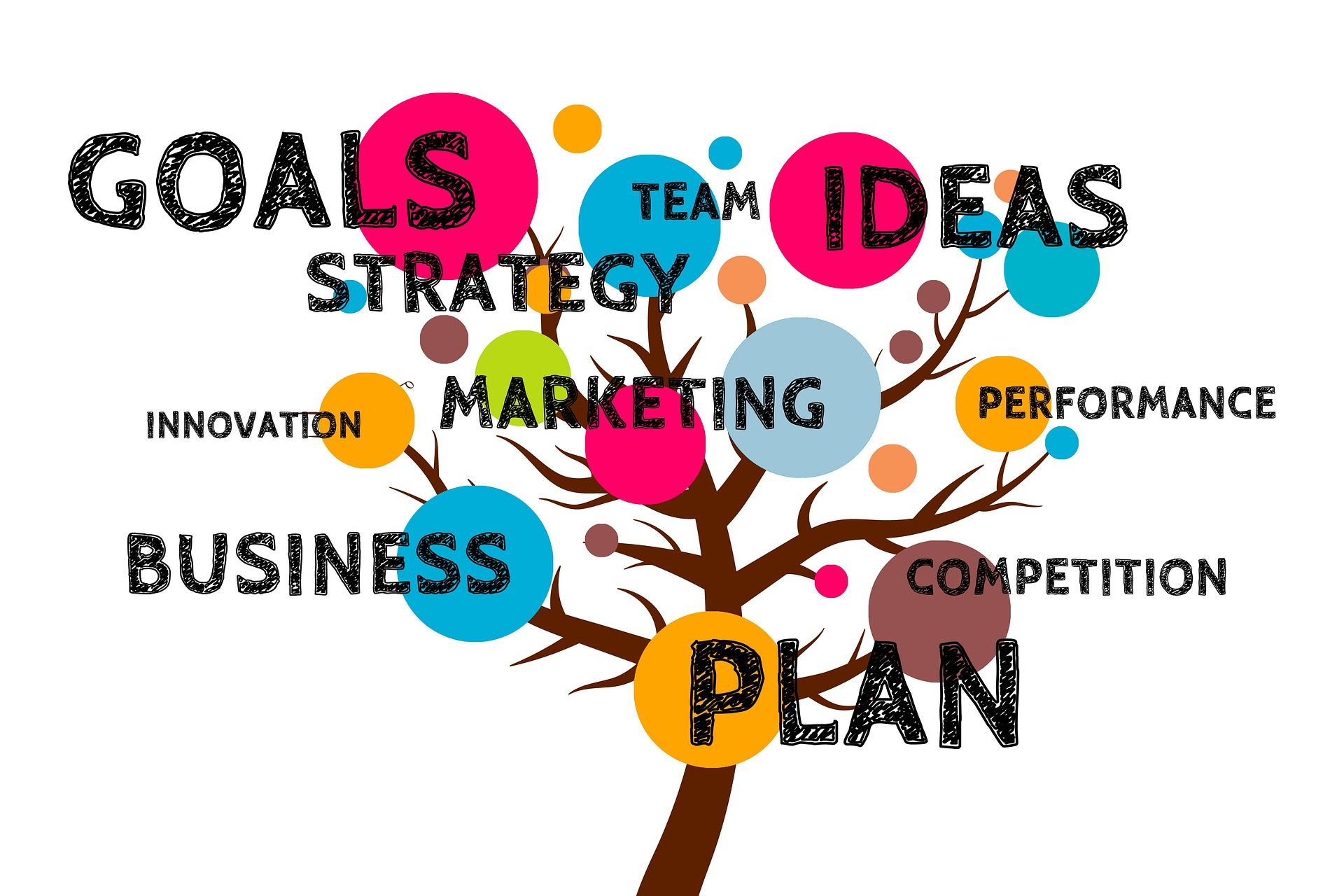
Manufacturing companies employing AI
According to research, 34% of manufacturing leaders are investing in AI while 19% in ML-based activities. Let’s have an outlook of the smart manufacturing companies relying on AI to improve the efficiency of their overall process:
BMW– BMW group is employing AI in its manufacturing process. In the ongoing process, the component images are evaluated in the production lines with the help of AI to ensure that the ongoing production is not deviating from the standard. At the time of final inspection, the order data of the vehicle is compared with the live image of the newly produced car. If the live image deviates from the order data, a notification is automatically generated to the team of final inspection for further measures.
Nissan – is using AI to design its new models. The objective of Nissan is to cut short the time-to-market for its model series of next generation. The program named “DriveSpark” is used by Nissan designers to produce exclusively new models compatible with the most recent regulatory and compliance requirements of the industry. AI is also being employed to enhance the life of existing models.
Caterpillar – The Marine sector of Caterpillar has started implementing machine learning to analyze data on when to clean hulls for maximum efficiency. After employing ML, its annual saving has reached up to $400K on each ship.
Thales SA – an electronic system supplier is employing ML for predictive maintenance of rail lines across Europe. Thales SA assembles past and present data from numerous sensors and train parts. By using this data, the company has produced an AI algorithm that helps in anticipating potential issues and proposing the replacement time for specific parts.
Nokia has recently announced an AI-based video application. This application finds the incongruities in the production process and issues beforehand warnings to the assembly operator to correct the issues in real-time. A wide range of variables influences the production process that humans find hard to analyze. Contrary, AI, and ML have the potential to predict the influence of each variable with more ease.
Schneider Electric has produced an AI-based analytics solution to expand worker safety, cut short the overall cost of the process, and attain sustainability goals. ML capabilities also help in boosting efficiency and saving time. By deploying Azure's ML-based solution, the operational efficiency was boosted by 10-%-20% in just a couple of days.
Canon is employing AI to improve the quality control of its manufacturing centers. It has introduced the system of Asset Defect Recognition in which it is integrating human insight with AI techniques to analyze images and detect the anticipated defects automatically, even those that the human eye can oversight.
General Motors is employing assembly robots with cameras mounted on them. The camera images help in identifying signs of a failing robotic component. In its pilot test, this AI robotic system identified 72 cases of component failure among 7000 robots.Hence, it helped in spotting the problem before occurring and prevented unplanned outages. Hence, in the manufacturing industry, AI is used for intelligent maintenance.
General Motors in collaboration with Autodesk is employing generative design algorithms in manufacturing. These algorithms use ML techniques to figure out the design constraints and propose an ameliorated product design. AI helps in achieving the objective of rapid prototyping. General Motors implemented Autodesk software of generative design to optimize the criterion of weight. The solution was examined with a prototype of a bracket part of the seatbelt. With the help of this AI-based software, the weight of a single-piece design was reduced to 40% with 20% extra strength than the original design of eight components.
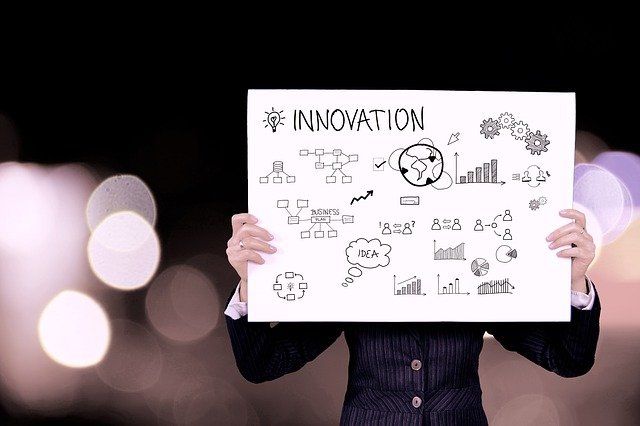
Wrapping Note
Manufacturing is one of the most prominent industries worldwide getting benefits from AI to its fullest potential. Today, the innovative manufacturers are pivoting toward data-driven operations, predictive analytics, digitization, and automation through AI to get the benefits including product quality by autonomous defect detection, machinery maintenance through predictive analytics, supply chain management through AI-driven Demand and Supply forecasting, and many more. With AI adoption, the manufacturers can optimize manufacturing processes and reduce the overall cost by making prompt decisions hence AI is proficient to create the best products at a cheap price. It also results in a cheaper price of the product for the customer. Moreover, by embracing AI technology and ML, the manufacturers can improve their output and efficiency by predicting demand fluctuations of the market, decreasing the number of unexpected events, and improving workforce safety. Simply put, the implementation of AI will continuously boost the revenue for a manufacturing company.
Keeping in view the huge potential, AI can be truly said the heart of the manufacturing industry, augmenting overall productivity while staying eco-friendly at the same time.
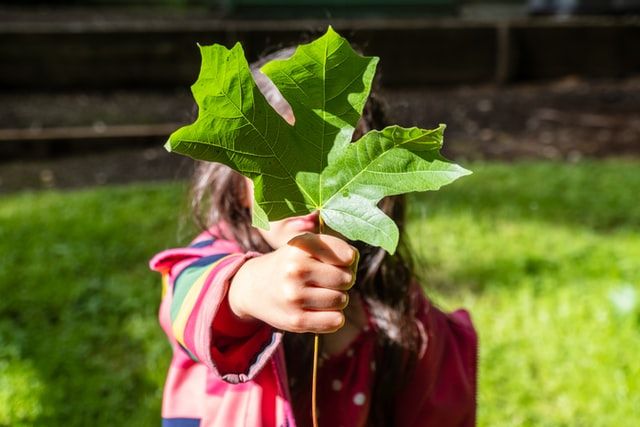